CN115786997B-electrolytic copper foil and preparation method thereof, anode electrode piece, secondary battery.
Application date: 2021-09-10
Publication (Announcement) Date: 2023-08-25
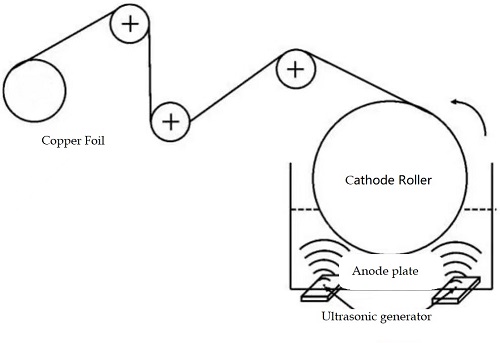
Electrolytic copper foil pile
Technical issues
The copper foil currently used mainly includes calendered copper foil based on calendering process and electrolytic copper foil based on electroplating process.
Calendered copper foil production technology requirements are high, the process is complex, the cost is high, and it is not suitable for large-scale production, so people gradually shift the research focus to electrolytic copper foil.
However, in order to meet the current high-quality energy density requirements of secondary batteries, electrolytic copper foil must be thinner and ensure sufficient tensile strength and hardness.
The mechanical properties of the existing electrolytic copper foil can no longer meet the requirements of high-quality energy-density secondary batteries, and wrinkling, broken bands, etc. often occur in the cold pressing process of the anode electrode piece, which greatly affects the production efficiency of secondary batteries.
Technical means
A method for preparing electrolytic copper foil of the present invention, the method comprises the following steps:
- S10, the anode, the cathode to be plated is placed in the electroplating bath including a twin growth agent plating solution.
- S20, DC plating is carried out under the condition that the plating solution is accompanied by one or both of f11 frequency ultrasound, f12 frequency ultrasonic and one or two random alternating conversion of f21 frequency ultrasonic and f22 frequency ultrasonic to obtain electrolytic copper foil, wherein: f11>40kHz,15kHz< f12≤40kHz, 0kHz<f21≤15kHz, f22=0kHz.
Example
(a)
Configure electroplating solution: copper sulfate, sulfuric acid, sodium chloride, twin growth agent, leveling agent, glossing agent dissolved in water, and fully stirred and mixed evenly.
The concentrations of each component are: copper ion 75g/L, sulfuric acid 55g/L, chloride ion 35ppm, twin growth agent 85ppm, leveling agent 30ml/L, glossing agent 20ml/L.
(b)
DC plating: At 25±5 °C, the anode plate and the cathode roller to be plated are immersed in the electroplating solution, and two ultrasonic generators are placed at the bottom of the electroplating tank.
DC plating is performed under the condition of ultrasonic wave, the current density is 30A/dm2, and the total plating time is 45min.
In the electroplating process, the ultrasonic frequency conversion scheme is: 28kHz-45kHz-28kHz-0kHz-10kHz-45kHz.
And the frequency conversion is carried out multiple cycles in turn, the total frequency conversion number is 269 times, and the proportion of ultrasonic time under different frequency ultrasonic waves: 15% – 20% – 25% – 5% – 15% – 20%.
The thickness of the electrolytic copper foil obtained after electroplating is 6μm.
Technical effect
The preparation method of electrolytic copper foil of the present invention can grow nano-copper structures with (111) crystal plane highly preferred orientation in different directions at high current density, which improves production efficiency while making electrolytic copper foil have higher isotropy and twin content, as well as better conductivity and mechanical properties.